Shop Balancing
Static Balance
A state of balance existing in a rotating body when there is coincidence between its center of mass and its axis of rotation, so that the body is in neutral equilibrium under the action of standing forces.
Dynamic Balance
A state of balance of a rotating body wherein its weight (mass) is so distributed about the axis of rotation that there will be no tendency to displace the axis of rotation when running.
To illustrate the between static and dynamic balance, see figure 1, a disc on a shaft resting on knife edges. The unbalance, W, acted upon by the force of gravity causes the assembly to roll until the weight is at the bottom. This is static, or force, unbalance.

Figure 1
The disc can be brought into balance (figure 2) by removing weight W, or by adding a similar weight at a point opposite the original unbalance and equidistant from the center of the shaft.
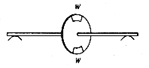
Figure 2
In figure 3 there are two discs on the shaft. The unbalance in one disc is exactly compensated for in the other, so the assembly is in static balance...but dynamically (rotating) it is badly out of balance.
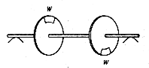
Figure 3
The centrifugal forces acting on this rotating assembly will tend to displace the axis of rotation as shown in figure 4. The ends of the shaft, unrestrained, would describe cones. Held fast by bearings the moment unbalance would cause vibration and noise and undue bearing wear. This form of dynamic balance is called couple.
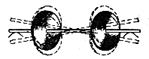
Figure 4
Changes in weight and in the planes where required or where practical, will eliminate both force and couple in any motor (figure 5). Knowing exactly where to make the weight changes is the precise art of balancing.
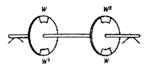
Figure 5
In-Place, Two-Plane Balancing
Cross effect must be taken into consideration when balancing in two planes. In the past, it has been very difficult to perform a precision two-plane balance in the field. Overhung rotors are the most difficult. With our vast experience and the technology of our vibration software and hardware, in-place two plane balancing has become routine.

Force - The calculated force caused by residual unbalance: F=1.77 x (rpm/1000)2 x ounce inches residual unbalance. This force becomes the load factor in the L-10 life of the bearing: L-10 Life= (16,666/rpm) (RtaingB/LoadE)3
Machinery Balance Conditions
Machinery components are typically balanced by the manufacturer to an ISO quality level of G6.3, unless otherwise specified by the customer. Some manufacturers are supplying dynamic balanced parts at lower quality levels. You should request this information from the manufacturer for your maintenance records.
It is our recommendation to request components be two-plane balanced to below the ISO quality level G2.5, ISO G1.0 is preferred. It is important to note that your vendors may charge more to achieve these balance conditions.
Interested in ISO quality levels? This chart breaks them down.
We use five state-of-the-art balancing machines to provide balancing capability of weights less than one pound up to weights greater than 25,000 pounds. All rotors are balanced to ISO quality level G1.0 as compared to typical manufacturers specification of level G6.3.We can also balance any part to customer specified levels.
Our 25,000-pound balancing stand is portable and can be set up at your location for balance of large rotors.
Beyond the typical fan, pump impeller, and motor rotor balance we have provided information to assist in the development of prototype rotors. We have balanced several high-speed, lightweight rotors requiring weight removal of less than 0.1 grams. We have setup our portable stand throughout the U.S. providing balance of large turbines, generators, and gears.